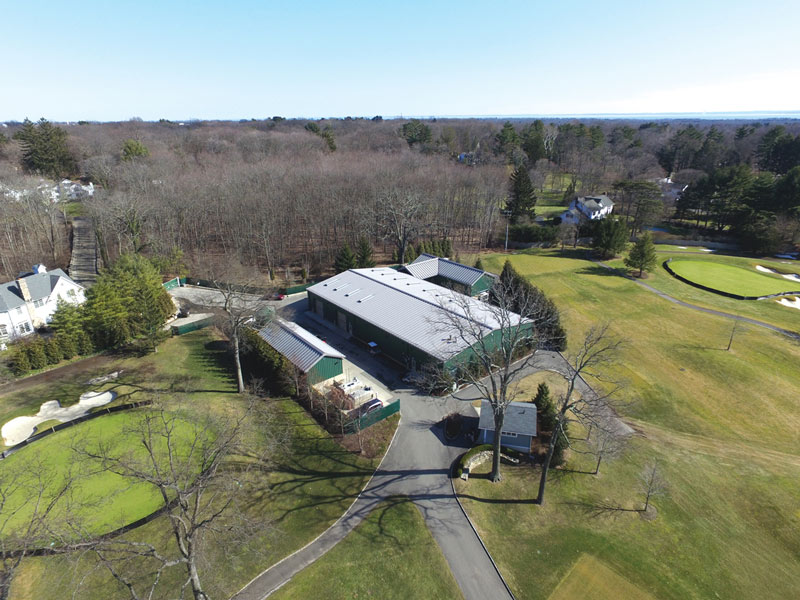
An aerial view of the 14,000-square-foot maintenance facility at The Country Club of Darien in Darien, Conn. The new building was completed in 2010. Photos courtesy of Tee to Green
Editor’s note: This article was originally published in the May/June 2019 issue of Tee to Green, a publication of the Metropolitan Golf Course Superintendents Association, Elmsford, N.Y.
No matter what shape or size your new golf course maintenance facility is destined to be, it will undoubtedly come with its own set of hurdles, particularly in regard to selling the idea to your club. To help you get off to the best start and then avoid some of the unanticipated pitfalls that can arise when building a new maintenance facility, we spoke with six superintendents who have been there, done that. What follows are their experiences, from selling to execution.
We hope these personal testimonies will serve you well as you set about showing the powers that be at your course that a new maintenance facility is not just a nice-to-have capital expenditure, but rather a proven necessity for running a productive and efficient maintenance operation.
Tim O’Neill
The Country Club of Darien
Darien, Conn.
Our original maintenance building was a tired, 30-year-old facility that was inadequate in just about every way. It was only 5,500 square feet, and its lunchroom and lockers could barely accommodate eight employees, let alone the 18 crew members we now have on staff.
In addition to being undersized, the building was environmentally challenged. There was poor ventilation for workers, especially those involved in mower sharpening. It also lacked fire protection and adequate material storage, pesticide storage and handling, and stormwater runoff and equipment wash areas.
After many discussions and meetings with club members combined with numerous and repeated consultant recommendations, the club recognized that it was time to modernize the maintenance facility. Eventually, the maintenance building became part of a much larger capital project. The club voted to replace the maintenance facility at a time when the golf course was being renovated, the staff house replaced, and the clubhouse, roads and parking lots revamped. Overall, the approval process with the membership took more than a year to complete.
We broke ground in September 2009, and by June 1, 2010, our brand-new, 14,000-sqaure-foot maintenance facility was finished. It included state-of-the-art equipment storage and washing facilities, up-to-date chemical storage, handling and cleaning capacity, a dedicated, ventilated room for mower sharpening, and a comfortable lunchroom and office as well as locker facilities for the entire staff.
In our case, the new maintenance facility was built in the same location as the old building. Therefore, we had to build a temporary facility to use from Labor Day to Memorial Day. We constructed the facility in our driving range on a paved surface that included three large storage containers, two tension fabric structures and two trailers that had electricity, potable water and heat. We also transported our equipment lift from our main facility along with an air compressor. Everything was completely fenced in for privacy. This was a major undertaking that was made all the more challenging because the golf course was still busy for many of those months and routine winter equipment maintenance had to continue.
Also important to be aware of is that the move from a temporary facility to a new building is not easy. We moved at the end of May, in the midst of our busy time on the golf course, and moving is disruptive, time-consuming and labor-intensive. We learned to work out of boxes and containers that first summer. It actually took almost a year to be fully comfortable with the new building setup.
The project was well worth the time and effort. Today, the members — and our employees — are very proud of our maintenance building, which continues to serve the club’s maintenance needs.
Resources:
Architect: David Woods of Culpen & Woods Architects, Stamford, Conn.
Site contractor: United Construction & Engineering Inc., Litchfield, Conn.
Engineer: AKF Engineers, Stamford, Conn.
Matt Severino
Scarsdale Golf Club
Hartsdale, N.Y.
We began construction in the fall of 2016 and opened our new maintenance facility at Scarsdale Golf Club during the summer of 2017. All told, the project took nine months.
The old maintenance building had been rebuilt after a fire many years before and was extremely inadequate. The entire complex was less than 3,000 square feet! There were no special areas for petroleum, chemical or fertilizer storage, and much of the equipment was permanently stored outside because of the lack of interior space. The maintenance shop had one small bathroom that was used by the grounds staff as well as by members as a restroom pit stop.
We started the sales process by visiting a few area clubs that had completed maintenance facility projects similar to the one we were envisioning at Scarsdale. We wanted to get their input on cost and challenges, and any suggestions on what they would do differently. Making sure we were informed on the details of the process was an important first step in selling the idea to the membership.
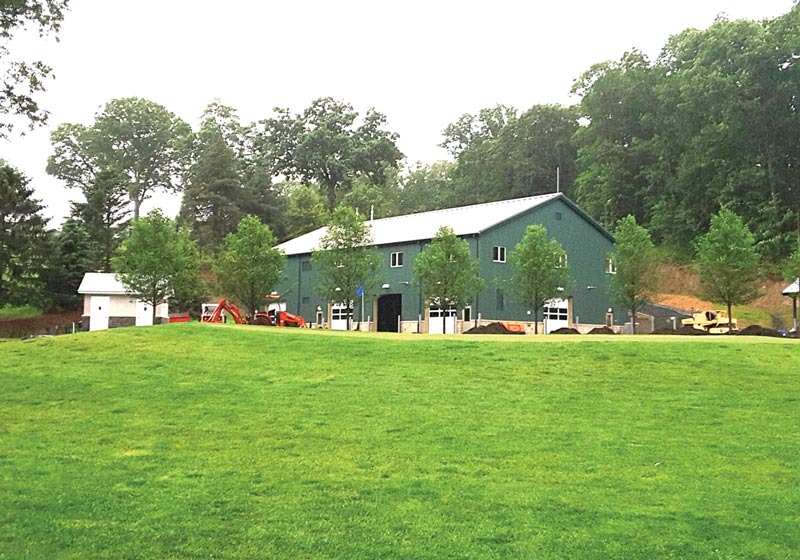
The upgraded, 12,000-square-foot maintenance facility at Scarsdale Golf Club.
We began our formal sales pitch for a new facility by offering a couple of member tours of our existing building and hosting Q&A sessions. Once everyone was well aware that the facility needed major improvements for both the safety and functionality of the operation, the membership approved the project by a more than two-thirds majority, which is an exceptionally high number for this type of project.
What seemed like a relatively easy sell, though, encountered a few snags. The project had originally been slated to be done in conjunction with two other capital projects, but it was put on the back burner because of cost overruns. The challenge became making the finances work in conjunction with the market correction and a backlog of other projects that were “sexier.”
The hardest part, however, was convincing not just the board and the general membership but also convincing myself that the cost of this type of project was truly justified. Fortunately, our architectural firm, James G. Rogers Architects, was instrumental in helping sell the project. Having built numerous maintenance facilities in the New York metropolitan area, they were well equipped to field any questions in addition to designing a superb facility.
Another thing I found really helpful in smoothing the way for the renovation project was that the club appointed a member to become involved in the planning, bidding, value engineering and financing details of the project. Once this person had gotten up to speed on all the complexities of the project, he was able to assist us with communicating the details, issues and challenges to the board and the general membership. Also invaluable was that we assembled a panel of members who were either in construction, architecture, real estate or engineering to help educate the rest of the membership and serve as credible sources of information concerning the project.
Our new maintenance facility is 12,000 square feet and is outfitted with an environmental center for storage of fertilizer, chemical and petroleum products; an equipment wash station; an employee locker room and break room; and a new member restroom and comfort station.
In the end, the time and effort we spent communicating with and educating our membership made all the difference in the perception of the project and in the support we received throughout it.
Resources:
Architect: James G. Rogers Architects, South Norwalk, Conn.
Engineers: Evans Associates, Bethany, Conn.; and Tietjen Venegas, Rye, N.Y.
Steve Rabideau
Winged Foot Golf Club
Mamaroneck, N.Y.
We started our project in 2017 and are scheduled to complete our new turf care facility in October. When all is said and done, the facility will be 39,000 square feet, which is fitting for a facility that has to accommodate 57 employees and two golf courses. The new building will be equipped with radiant heat in the repair shop, an indoor wash bay for equipment, a Carbtrol wash system, and a backup generator for the entire turf care facility.
Getting the go-ahead on a new maintenance facility was no easy task. It took four tries over the course of six years. As is the case at most clubs, funding a new maintenance facility was low on the priority list at Winged Foot. Few members had ever even seen the facility, let alone understood what it takes to run a grounds maintenance operation safely and efficiently.
What finally clinched the deal was inviting the green committee and club president to a presentation in the old maintenance building. Upon taking the not-so-grand tour, they were appalled by what they saw and agreed that a new facility would be a more-than-worthy investment.
The next step was to sell the new maintenance facility to the entire membership. What helped was that our building project was bundled with a few others — including a dining room renovation — that were sure to be well received. Because the members’ vote was for all or nothing, our building proposal passed with flying colors.
I have learned a lot throughout this process. If I were to do it over again, I would have asked a lot more questions, and I would have built in a more sizable contingency number than I did. We had several unexpected change orders that I might have been able to avoid had I pressed the contractors for more detailed information.
The other lesson I’ve learned is that building a new turf care facility in the same location as the old one is challenging. We are phasing the project over an almost two-year period, which is very difficult and costly. We underestimated a number of expenses we would incur during the different phases of the project that were necessary for us to operate at full capacity and not miss a beat on the golf course. For instance, because we’ve had to shift from one building to another to continue the various aspects of our operation throughout the project, we needed almost constant assistance from an electrical contractor to hook up power to these temporary structures. It was an unanticipated part of the project that resulted in many change orders and a significant added expense.
But, as they say, hindsight is 20/20. Don’t be afraid to ask probing questions about every step of the process before you sign on the dotted line.
Resources:
Architect: Rogers McCagg Architects, Norwalk, Conn.
General contractor: Claris Construction, Newtown, Conn.
Site contractor: Cortese Construction, Yonkers, N.Y.
Engineer: Tietjen Venegas, Rye, N.Y.
Paul Gonzalez
Whippoorwill Club
Armonk, N.Y.
Our new maintenance facility was built in 2015. It took a full year to complete and had taken 10 years to get approved. My first green chairman, who was in construction, had tried to start the ball rolling. He saw that we were operating out of three inadequate locations: one 2,000-square-foot pole barn, which had a tiny heated area for the crew and the rest for equipment storage; a space below the cart barn, which was allocated as a garage for the mechanic; and a small trailer for my office, where we would convene now and then for staff meetings. He recognized that we needed to invest in the infrastructure of the maintenance operation, but his testimony still couldn’t inspire action.
Even with the obvious inadequacies of the current facility and the fact that the new facility could be built without a member assessment, it was still a tough sell. It wasn’t until the powers that be joined me on a tour of some of the new and improved facilities in the area that they recognized just how deficient ours was in every way. Probably the biggest selling point was that everyone realized we had no choice but to bring our facility up to code. Fortunately, one of the board members was vice president of a construction company, and when he spoke, everyone listened — the members, contractors, engineers and architects. He knew what to ask, and he held everyone accountable with weekly meetings.
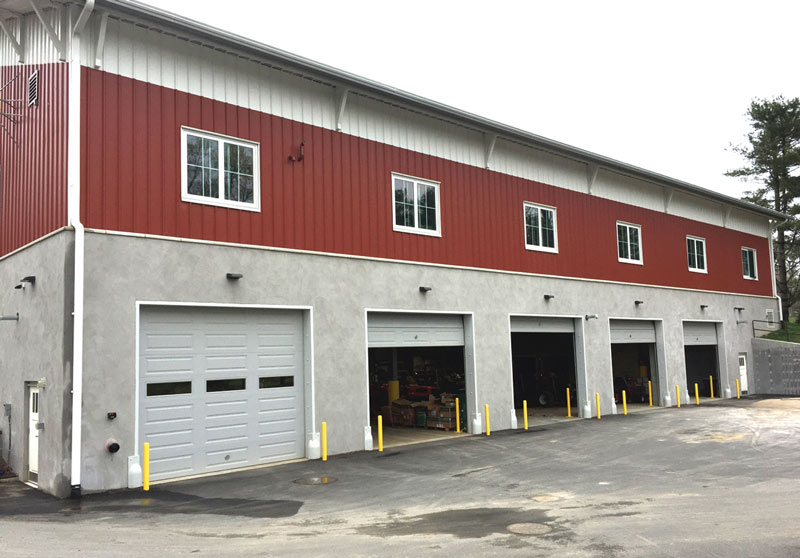
Three former maintenance operation locations at Whippoorwill Club were merged into this one state-of-the-art, 15,000-square-foot facility that includes an additional 2,000 square feet for chemical storage.
One thing I learned from completing this project is that there are always bound to be surprises, and they’re often things you couldn’t have anticipated. In excavating the site, for instance, we hit far more rock than we ever thought possible, and that of course led to cost overruns.
I also realized that even if you think you’ve started the permitting process early enough, you probably haven’t. It took us almost two years to secure our permit from the town’s planning board.
Next, don’t shortchange any part of the building process to save a few dollars. That was another advantage of having someone in the construction business watchdog our project — he saved us from having any regrets down the road.
Last but not least, I realize now that even if you build a large facility, it’s never big enough. Our facility is 15,000 square feet with another 2,000 in chemical storage, and we still have equipment outside. (Not that I’m complaining!)
Taking on a project of this magnitude is a lot of hard, slogging work, but there’s no doubt the juice is worth the squeeze.
Resources:
Architect: Sullivan Architecture, White Plains, N.Y.
Site contractor: Wernert Construction, Cos Cob, Conn.
Engineer: John Meyer Consulting, Armonk, N.Y.
Kevin Seibel
Century Country Club
Purchase, N.Y.
We built our new maintenance facility in 2014, but we had begun the approval process 11 years earlier. When I started at the club in 2003, my green chair saw that our facility was inadequate. It was a 5,000-square-foot cinder block building with two separate buildings that were used for cold storage, a maintenance repair area and sprayer equipment storage. Hundreds of thousands of dollars of equipment sat outside year-round, resulting in undue wear and tear on the machinery.
My chairman supported bringing a few members to see other area clubs’ newer facilities, but it wasn’t until years later, when our general manager, Burton Ward, supported the project that we finally got the go-ahead for our own new facility.
Once a year, the general manager would tour the property with the board of governors, and one of their stops would be the maintenance facility so they could see just how inadequate our facility was for a 23-person staff and the magnitude of our operation.
I also brought the facility’s inadequacies to their attention. The USGA was particularly helpful here. When Dave Oatis would visit the course, I would bring him to the shop, where he could view for himself the building’s many shortcomings and safety issues. He included these in his report to the club. I also emphasized to the club that the maintenance facility was a liability not just in terms of its safety issues, but also because it was so unappealing that it was driving current employees to quit and preventing prospective employees from taking the job. They could, after all, find clubs with more comfortable and better-equipped working environments.
This clinched the deal, and we broke ground in October of 2012, across the property from where our original building site was. This made things a lot easier, as we were able to continue our operation without constructing a temporary facility.
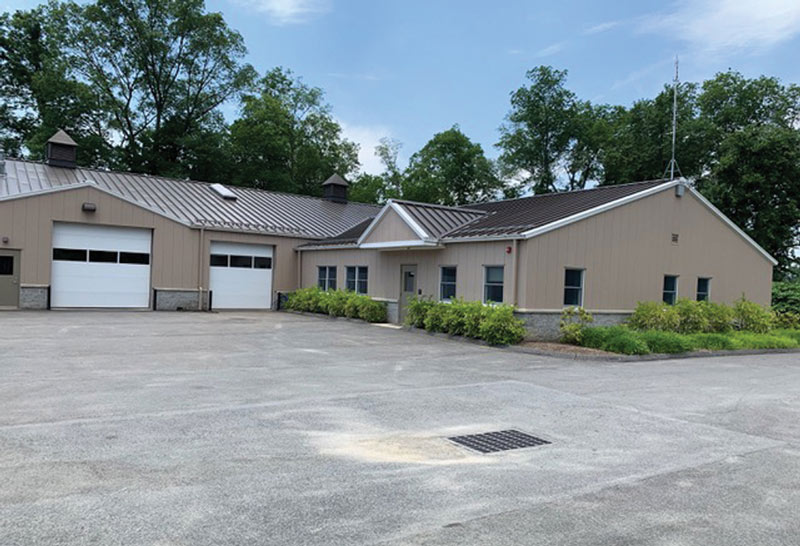
Century Country Club’s 18,000-square-foot maintenance facility features a drive-in basement.
The project took a year and a half from start to finish. Progress was delayed initially because of an issue with our original site contractor. Admittedly, we had a difficult site — our soils had high silt content, and we were excavating for a 6,000-square-foot lower level. This required more work than our initial contractor was staffed for. We had to hire a second contractor, Shawn’s Lawns, who got us back on track. Much of the project logistics were left to our general contractor, Lee Lasberg, and we would check in regularly with a subcommittee that included Lasberg, the general manager, my green chair, the club president and me. That way, there were no surprises.
Our new maintenance facility was completed in March 2014 and includes 18,000 square feet of floor space with a 12,000-square-foot footprint. The lower level is a 6,000-square-foot drive-in basement that houses all the utility vehicles and smaller equipment. The upper level includes large equipment, the mechanic’s repair area, and an administration area complete with offices, a break room and a locker room.
On the other side of the yard is an environmental center with a Carbtrol wash water recycling system and a Plant Star chemical mix and load plant. On each side are wash pads and gas and diesel storage tanks. Adjacent to the building are four covered bins.
When the project was finished, the club held a dinner and then shuttled members by bus to tour the new facility, where there was a full bar set up to celebrate the success of the project. Needless to say, all were impressed — not just with how the building was outfitted, but also with the cleanliness of the facility. As part of the package, we were given a dedicated employee charged with keeping all 18,000 square feet clean and orderly. He has been a great asset and one I would recommend to anyone with a sizable facility.
Looking back, I would emphasize that it’s key to have a good working relationship with your general contractor, because this may well be one of the most labor-intensive projects you’ll ever undertake — more labor-intensive than installing a new irrigation system or managing a course renovation.
And if I were to offer a lesson learned, it would be that you have to pay close attention to the instructions for finishing your shop floor. If you don’t apply the epoxy under the absolute proper conditions — the concrete must be 100% moisture-free — and according to label directions, you’ll find the paint will begin to peel within a few years. Redoing the finish is time-consuming and costly. It pays to have someone from the paint company advise you when the time is right.
In the end, the maintenance facility upgrade has been one of the best things Century Country Club has done. Aside from reducing the wear and tear on the equipment — one of the maintenance operation’s most essential assets — it has been great for staff morale and the efficiency of the operation.
Resources:
Architect: James G. Rogers Architects, South Norwalk, Conn.
General contractor: Lee Lasberg
Site contractor: Shawn’s Lawns, Stamford, Conn.
Engineer: Insite Engineering, Surveying and Landscape Architecture, Carmel, N.Y.
Nick Lerner
Bonnie Briar Country Club
Larchmont, N.Y.
Our original maintenance building was a 2,000-square-foot cinder block structure with a flat roof and no running water, which meant our only bathroom facility was a port-a-john. My office was in a rented trailer. Conditions were deplorable and a liability in every way. Pesticide and fuel storage areas weren’t up to code. Most of our equipment sat outside, exposed to the elements, and the pieces that were inside sat in an area that flooded regularly. Our mechanic would often have to stand in water to work on the equipment. Had a local government agency come in to inspect our facility, it would have required immediate remedial action and imposed significant fines — a costly proposition.
In early 2003, about six months before I came on board, the club had hired an agronomist, Ed Etchells, to consult. He had informed the club of the maintenance building deficiencies, as did the visiting USGA agronomist. The USGA gave the board and green chairman its literature on properly outfitting a maintenance facility. That was the start of the approval process.
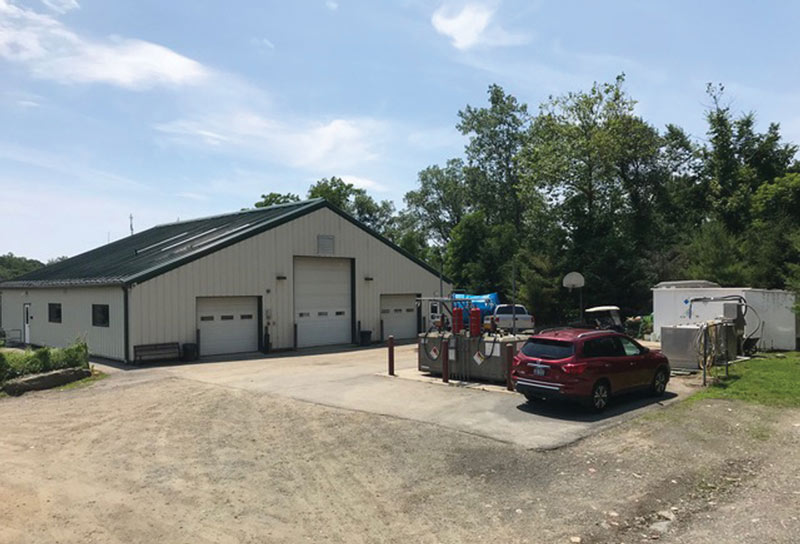
From highly inadequate to highly functional: Bonnie Briar Country Club’s 7,200-square-foot maintenance facility.
At that time, the club was also serious about elevating playing conditions, and they realized that if they wanted us to improve conditions, they would have to take what we do seriously and fund a new and improved maintenance facility. We would need more sophisticated equipment, which couldn’t tolerate being out in the elements, and we would need a facility that would promote pride among employees in their work while improving efficiency. A new facility would also be more apt to attract and retain the kind of staff who would be capable of taking the golf course to the next level. Everyone at every level enjoys a work environment that is pleasant and well equipped.
We broke ground in June 2006. One of the first things I did was stress that the club get an independent construction manager to rep the project. That way, there would be someone other than me who could manage the various contractors and subcontractors and watchdog their work to keep them on track and ensure they weren’t cutting corners.
The other positive step we took was holding what we called an “owners meeting” every two weeks. These meetings included a member representative who was involved with the project from the start, the club’s general manager, the construction manager, contractor, architect, engineer and me. We would hash out just about every aspect of the project, any unexpected expenses or change orders, and any schedule changes. Because we had a construction manager on board, I was free to focus more on running the course than on the day-to-day details of running the project.
By April 2007, our new, 7,200-square-foot maintenance facility — with separate chemical storage building, separate chemical fill station, petroleum storage tanks, equipment wash water recycle system and equipment lift — was up and operational. The facility is small, but it’s a far cry from what we started with.
And believe it or not, building a new facility has actually resulted in some cost savings. By having the ability to house much of our equipment indoors, we’ve seen a drop in the cost of repairs and equipment replacement. We have also eliminated the rental costs on the port-a-john and office trailer. We’re now able to purchase fertilizer by the pallet rather than by the bag, which also helps the bottom line over time.
All in all, the new building has been a win-win for the club and certainly for our maintenance operation.
Resources:
Architect: Butler Rogers Baskett Architects, South Norwalk, Conn. (Tony Panza was our day-to-day contact on this project.)
Construction manager: RBI Consultants Inc., New Canaan, Conn.
Site contractor: William A. Kelly & Co., Katonah, N.Y.
Engineer: TRC Raymond Keyes Associates, Hawthorne, N.Y.
Pandora Wojick is the managing editor of Tee to Green, a publication of the Metropolitan Golf Course Superintendents Association.