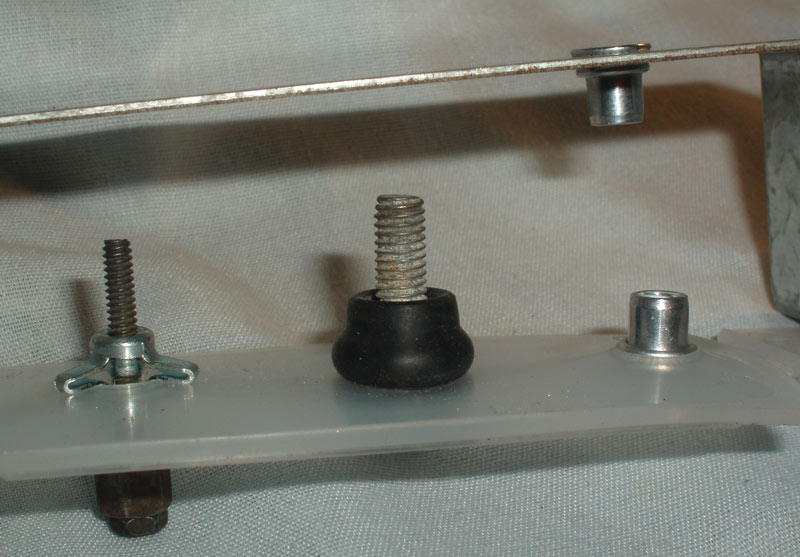
A rivet nut mounted in steel (top right), with a jack nut (lower left) and a rubber nut (center) both mounted in soft plastic. At lower right is a rivet nut that squeezed the plastic too tight, distorting the panel and easily pulling out when put under a light load. Photos by Scott R. Nesbitt
“Blind” fasteners give you a solid anchor on panels and plates, whether metal, plastic or fiberglass. They require more time and tools than sheet metal screws, but the benefits are worth it. They’re called “blind” because you need not see or touch the back side of the panel to put a nut on a bolt. Even if you can reach the back side, installing a blind fastener will give you a solid mounting point, likely saving you time and trouble.
When I used sheet metal screws to fasten the “D” ring cargo anchors in my pickup truck’s bed, the screws kept loosening. Installing ¼-20 rivet nuts (also called “rivnuts”) solved the problem. Installing some expanding rubber nuts (also called “well nuts”) and jack nuts gave me anchors in the cab for a cell phone holder and a trash bag mounted on the cab’s plastic dashboard and door panels. These accessories are attached with threaded fasteners that can be removed, unlike “pop” rivet blind fasteners that require drilling to remove.
Although blind fasteners are common in all manner of vehicles and home appliances, your local hardware store probably won’t have them. Do an online search of the terms above, and you’ll find them.
Glance at the photo above of the four anchors, and the concept is intuitive. For proper mounting, though, you absolutely must start by drilling a hole of the proper size. My blind anchor kit includes a drill bit gauge to find the hole size that best matches the anchor’s outside diameter. Too large a hole, and the anchor won’t grip enough of the panel to resist twisting.
No special tools are needed for the rubber well nuts, or for the jack nuts that have wings that easily open when a bolt is screwed in. These anchors work nicely in plastics and fiberglass, because they spread the load over a wider area.
Straight-sided rivet nuts take more force and some practice to develop a feel for. For aluminum rivet nuts up to ¼ inch in diameter, the hand-squeeze installation tool works well. For plain and stainless steel rivet nuts, you’ll need to assemble a simple installation rig. Take a steel bolt, slide a lubricated plain washer on, and then slide on a next-size-larger hex nut. Then slide on a lock washer, put a dab of oil or grease on the bolt threads, and screw on the rivet nut.
Put the rivet nut in the hole, grip the hex nut with an open-end wrench, and use a box-end or short ratchet wrench on the bolt head and start tightening. You’ll feel resistance at first. Resistance will decrease when the sides of the rivet nut start expanding. When the rivet nut’s threaded end touches the panel, you’ll feel the resistance increase. Wiggle the wrench holding the rig’s hex nut and tighten the installation bolt a bit, if needed, to make sure the rivet nut is gripping the panel firmly, then remove the rig.
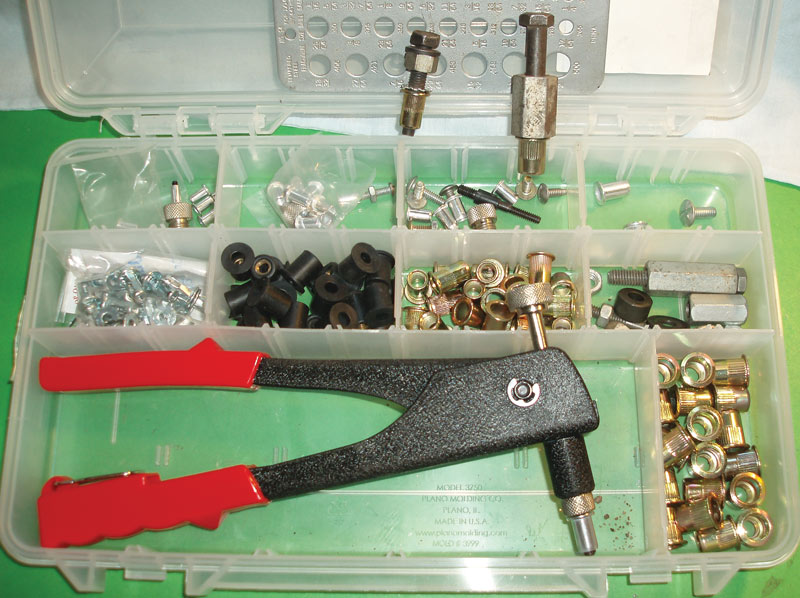
A blind fastener kit stocked with (at top) a drill size gauge and two “rigs” for installing steel rivet nuts, with parts for other rigs in the far right of the center bin. Silver-colored aluminum rivet nuts in the top bins are installed with the hand tool at bottom. Jack nuts are in the left of the center bin, next to black rubber well nuts. The brass-colored rivet nuts are steel and are installed using the rigs assembled from bits and pieces of the shop’s fastener supplies.
Because the rivet nut, rubber nut and jack nut have less “meat” than a standard nut, be careful when doing your final assembly. Don’t go crazy with tightening. Adding a lock washer or a bit of thread-lock liquid to the final assembly should help hold things in place. Excess torque can damage the internal threads, or can weaken or crack the panel material.
The kit I’ve assembled (for under $45) includes 6-32 jack nuts and aluminum rivet nuts in that size and 8-32, plus 10-24 and ¼-20 aluminum nuts, and steel rivet nuts in 8-millimeter and ⅜-16 sizes. The rubber nuts take a 6mm-1.0 bolt, the commonly found metric fastener that usually has a 10-millimeter hex head. That seems to cover every need so far, from mounting items on engine shrouding to customizing my truck.
Scott R. Nesbitt is a freelance writer and former GCSAA staff member. He lives in Cleveland, Ga.