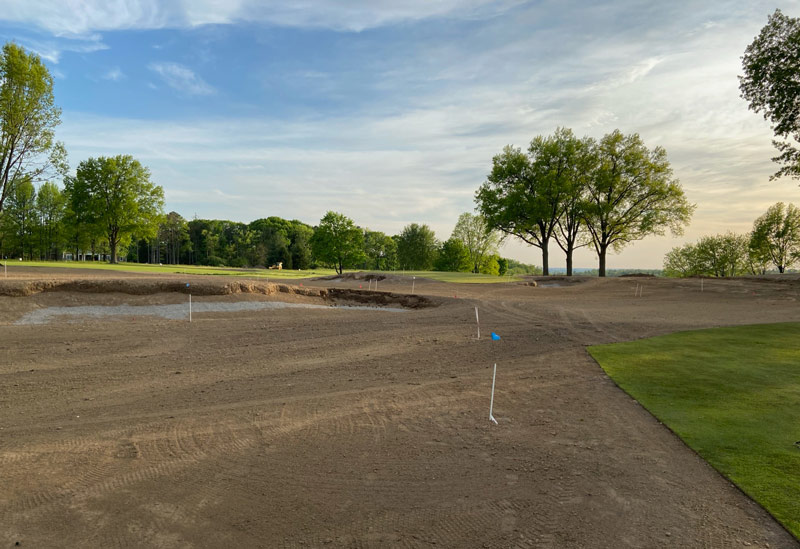
A view of the seventh hole of the Kendale Course at Kenwood Country Club in Cincinnati during recent renovation work. Bunkering has been restored, new irrigation installed, bunkers edged and drained, and the fairway prepared to be regrassed â a step the club would take an unconventional approach to. Photos courtesy of Kenwood Country Club
When Kent Turner arrived at 36-hole Kenwood Country Club in Cincinnati in 2014, he knew what to expect. Founded in 1930, the club had already initiated a long-term âcentennial project.â Major renovations were clearly in store, and Turnerâs hire was no coincidence.
The GCSAA Class A superintendent and 14-year association member had spent nearly 15 years at Brookside Country Club in Canton, Ohio, as an assistant, then as head superintendent. While an assistant, he had served as project manager on a comprehensive and quite celebrated course renovation. Golf Digest named it the top course renovation of 2005. When Kenwood Country Club retained architects Dana Fry and Jason Straka in 2018 to reformulate Kenwoodâs master plan, Turner â only the third superintendent Kenwood CC has ever hadâ was determined to put his experience to good use.
Fry/Straka Global Golf Course Design delivered a new master plan to Kenwood CC in 2018. In the fall of 2019, Straka and crews from Wadsworth Construction broke ground on the Kendale Course, the clubâs championship 18. And thatâs where Turner left his previous renovation experience behind.
Instead of playing the traditional superintendentâs role during a renovation â that of advising and assisting where appropriate, and, in this case, tending to the 18 holes at Kenwood that were not being renovated â Turner and his crews worked alongside Straka and Wadsworth to a degree that was decidedly nontraditional.
The new greens on the Kendale Course, for example, were recontoured â not cored out and rebuilt. Thereafter, they were largely regrassed with existing sod from other greens on-site. Turner was confident the process would save the club significant money in sod and seed purchases and would also eventually produce more-consistent putting surfaces.
But Turner and the club didnât hire a contractor for this work. Turner and his crews tackled this project â a high-stakes, fast-moving, logistical exercise in robbing Peter to pay Paul. One green would be stripped, and that sod would be transported to another green that was ready for resodding. Turner and his crews replicated this sod-stripping, sod-moving and sod-laying exercise for all the courseâs fairways and tees, too.
âIt kind of was an ongoing conversation between myself, Jason and the greens chairman, against a backdrop of trying to keep this project under budget,â explains Turner, who departed Kenwood in July to join the agricultural science company FMC Corp. as a turf and ornamental field specialist. An immediate past president of the Greater Cincinnati GCSA, Turner will remain a trustee with the Ohio Turfgrass Foundation.
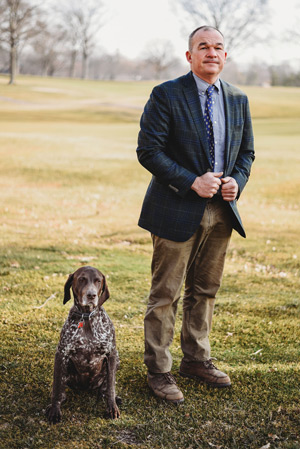
âWe had this renovation budget number we were holding on to â $5 million,â says Turner (pictured at right, with Crosby). âWe knew the various things we wanted to get done from a value-engineering standpoint, and our in-house role just grew as a means of meeting the number. We had the unit prices of reseeding, resodding, buying sod, and stripping and replacing the greens. We just moved those numbers around until we met our budget â and what that ultimately meant was picking sod up and moving it from one place to another place. Over and over again.â
This sod shuffle wasnât the only cost-saving measure. Turner also assumed a de facto project management role during construction â effectively separating the contracting role from the material-purchasing role â to better control expenses. In addition to flipping sod, Turnerâs maintenance crews also rebuilt a dam, installed bunker liners, and removed some 1,300 spruce, sweet gum and oak trees.
âKent did the clearing, the sod stripping and laying, the silt fence installation and removal, some drainage, irrigation, and more,â Straka says. âI actually went back to a spreadsheet we created when bids came in for the work he was going to take on. It was $600,000, plus the clearing, which was another $900,000. Thatâs a total ballpark savings of approximately $1,500,000.â
When all was said and done, total project costs finished up at $4.95 million, according to Turner.
A tale of two architects
Ground was broken on the Kendale Course following three years of careful preparations and master planning. The renovated Kendale layout had been poised to fully reopen last summer, but COVID-19 intervened. Members enjoyed some limited play in the fall of 2020, and an official members-only celebration of the revamped course was held on May 22, 2021.
âWe experienced just enough of a sneak preview last fall to knock everyoneâs socks off,â says Kenwood CEO Dylan Petrick. âStill, the board, Kent Turner and our new director of golf, Shawn Costello, all agreed the renovation would not be fully realized until this spring, when the growing season is over. I think the members always knew we had the bones of a world-class, vintage golf course here. But what Fry and Straka have uncovered, revived and created here with Kent is pretty extraordinary. We canât wait to show it off.â
The original 36 at Kenwood Country Club was designed by architect Bill Diddel and opened in 1930. The club had retained Donald Ross two years prior. Ross is, in fact, responsible for identifying the 341-acre property on which the club sits today. But Ross wasnât hired to design the course. No one is quite sure why, Petrick says. And no one is complaining. Diddelâs work proved a spectacular and immediate hit: The Kendale Course hosted the U.S. Amateur just three years post-opening, followed by the 1954 Western Open, the 1963 U.S. Womenâs Open, and dozens of prestigious regional events.
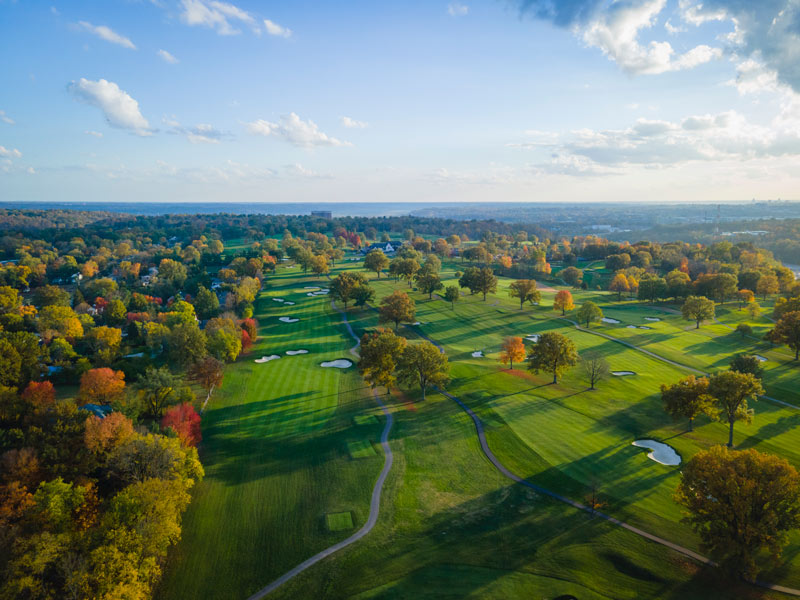
A refreshed Kenwood Country Club in fall 2020, the year of its 90th anniversary.
Diddel is, in fact, one of the unheralded heroes of golfâs Golden Age of course design. The Indiana native laid out more than 250 courses across the Midwest. He was a founding member of the American Society of Golf Course Architects (ASGCA), in 1947, and a member of the Indiana Basketball Hall of Fame.
âRoss was great, but he canât compete with Bill Diddel from a basketball perspective,â says Jason Straka, cracking a wry smile. Straka is a partner with Fry/Straka and will serve as ASGCA president beginning in fall 2021. âIn a very real way, Ross and Diddel collaborated at Kenwood. The land Ross chose here, for what became the Kendale Course, is absolutely perfect for golf â just the right amount of roll, with some extraordinary vistas. Diddel did the rest.â
In enacting Strakaâs master plan, Straka, Turner and Wadsworth expanded all 18 putting surfaces to their original dimensions. To do so, they first employed lidar technology â âlight detection and ranging,â which uses laser beams to createâŻmodels of ground elevationâŻand measure an objectâs distance from the Earthâs surface â to map the original contours down to one-tenth of an inch. Then, using Diddelâs original greens drawings, Straka proportionally adapted those steeper contours to work with modern green speeds.
âThe ninth at Kendale used to have just three hole locations. Three!â Straka says. âToday, the ninth can accommodate at least 12 places to cut a cup. Most of the members at Kenwood donât even remember the pin placements weâve brought back into play. The slopes had become so severe, on account of modern green speeds, folks hadnât played to those hole locations in 30 or 40 years. Now they can.â
And yet, according to Turner, âWhen I drive up and look at the second green today, or the 15th, they look like absolutely nothing in terms of contour has changed from five years ago. Amazing.â
Not just new greens
Turner and Straka chose not to re-core all 18 greens. That was, however, pretty much the only limitation to project scope. The renovation of the Kendale Course included:
- Removal of more than 1,300 trees
- Four sightline cuts for improved green visibility
- Contour softening on 13 greens
- Relocation of three greens
- Construction of a new chipping green
- Installation of 24,000 linear feet of field drainage
- Installation of 123,417 linear feet of slit drainage
- Installation of 100 water inlets
- Addition of 81,350 square feet of tee space
- Replacement, relocation and addition of bunkers, increasing the Kendaleâs total bunker footprint by about 24,000 square feet
- Regrassing of all 18 green surrounds
- Addition of chipping swales around each green
- Expansion of fairway widths
- Installation of a new irrigation system
- Addition of a bridge to cross the pond at 10 and 11
- Improvement and stabilization of the pond edge at 10 and 11
And this factoid bears repeating: Turner and his crews work at a 36-hole facility. The Kenview Course, experiencing more play than ever, naturally had to be maintained throughout the Kendale renovation. Such was the context for Turnerâs âside gigâ as renovation project manager, where logistics were mainly executed at a momentâs notice.
âIt was a daily audible call between myself and the Wadsworth site superintendent, Qui Fabian,â says Turner. âWeâd meet each morning and Iâd ask, âWhere are you going next, so we can do [fill in the blank].â Their subcontractor moved a lot of sod, but we moved a lot in-house, to salvage what we could and reduce the amount weâd have to purchase. Bent sod is really expensive. So, if there was a bunker they rebuilt and they werenât redoing fairway, weâd jump in there, grab and preserve what we could, to reduce the bent sod buy.
âMy crews had moved two greens back on another project, in 2014, so we had a system, and we were already good at it. Weâd get started stripping and rolling in the dark, before the sun came up. Weâd either set the sod aside for the moment, on plastic, or immediately move it to another hole once weâd rolled it onto 3-foot, 2-inch PVC pipe, in 10-foot spans. We had a rolling crew and an unrolling crew. My one project regret: I didnât set up a GoPro over one of the greens, on time-lapse. I actually did set one up, but it didnât record! That video would have been awesome.â
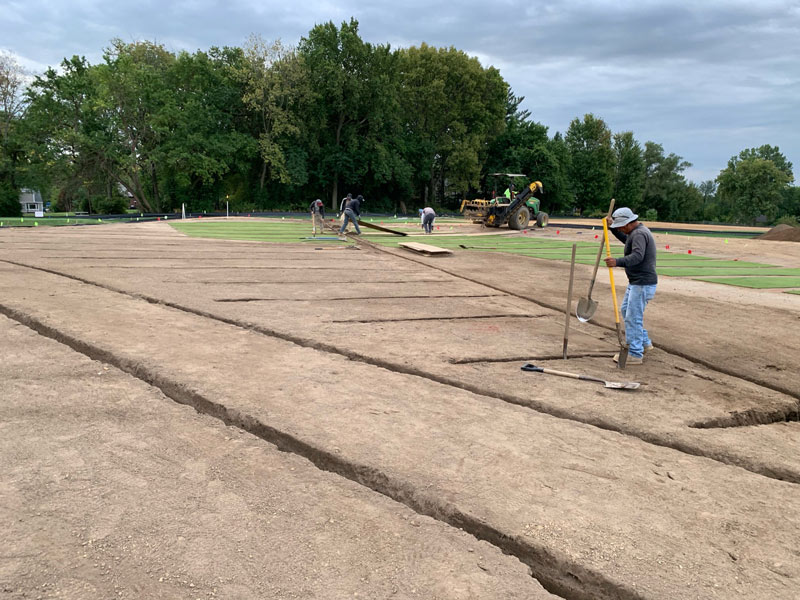
Drainage being installed on the third green of the Kendale Course after reconstruction and strategic contour softening.
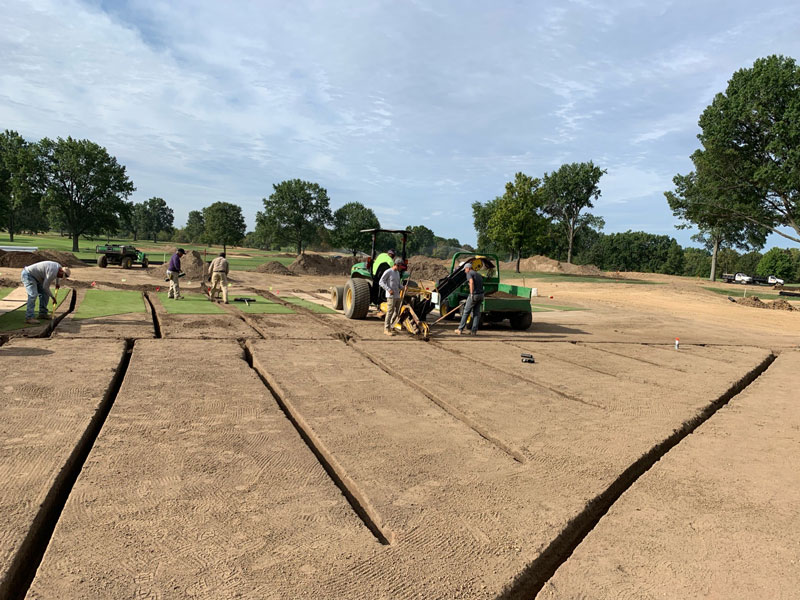
New greens drainage included 2-inch perforated tile and a backfill of a specialized mix that would drain but was not too dissimilar in soil characteristics from the original greens mix.
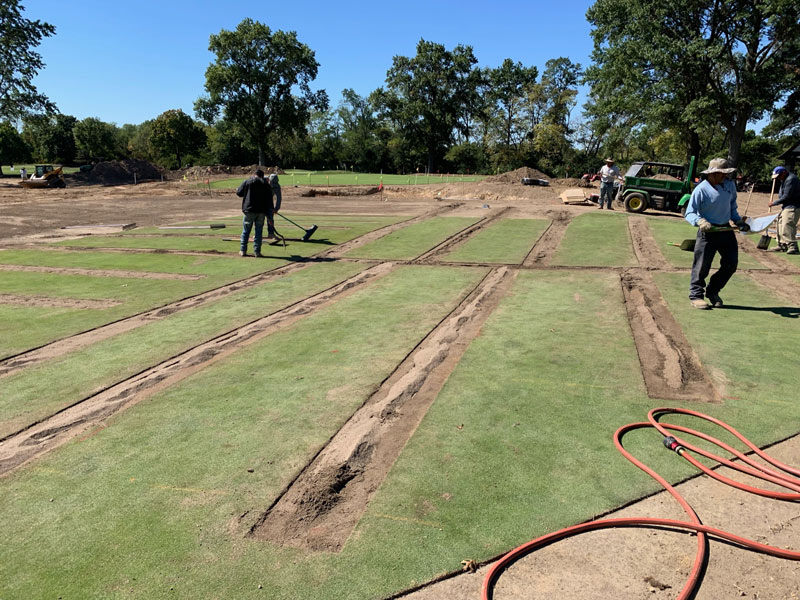
On greens not in need of softening, sod was stripped over the drainage lines, drainage was installed, and the sod was replaced.
At first, there werenât enough regraded or otherwise prepped greens, tees and fairways that required sod transferred from elsewhere on the site. So Turner and his crews stripped sod and stored it on plastic, in shady spots in the rough. Bent/Poa sod stripped from putting surfaces could survive indefinitely in that environment. Stripped fairway sod might only last a day without being rolled out, depending on the temperatures, so that sod was typically not stripped without a definite destination in mind.
But soon enough, there was so much demand for sod that little storage was required, and sod was usually stripped and immediately delivered. Somewhere.
âThat was crazy â to not know exactly where fairway sod might be going during the removal process,â Turner says. âThere was so much disturbance. The logistics of staying ahead of construction but not beating them to the finish line? Pretty intense. Greens generate about 5 acres, but fairways could be 15 and up. All the tees were sodded in-house, except for one or two. When we got near the end, we finally ran out of sod, because we added so much tee square footage as part of the renovation. So we purchased an acre and finished the tees.
âSome of the fairways were seeded, too â five of them, for the same reason. We just ran out of sod to roll over, so we seeded those areas. We knew that would happen eventually, because the master plan called for the widening and expansion of so many fairway corridors.â
All reused sod in the project was Poa annua/bentgrass, with the bentgrass being a mix of several varieties seeded over time. All new seeding was done with Declaration bentgrass.
Renovation reduces shade, Poa
Turner deployed the same general approach to relocating sod on the greens, but not right away, and not without eventually adding a twist. The plan at first? Strip the sod off a green, regrade the green, then put the same sod back on the green. Strakaâs master plan called for expanding each putting surface approximately 25%. For those expanded areas, Turner would use cores gathered from aerified greens elsewhere, mix them with bentgrass seed, and plant those to achieve full coverage.
âBut after I watched the first green regrassed in that way,â Turner says, âI got to thinking: Weâre going to have 18 different stages of grow-in going at one time, and later weâll have 18 different heights to manage. Thatâs when we decided to rob Peter to pay Paul on the greens, too.
âWe had four greens where we had already decided to go the core-and-seed route, because those four greens were going to be physically relocated. They could be stripped at any time. So their sod served the needs of other holes first, according to those schedules. But eventually we ran out of sod to harvest from other greens, too, so 3.5 greens were core-and-seeded on account of that. At one point last September, when we were partially open, we had five different heights of cut going out there on the greens â new sod, old sod and three stages of cores and seed. But ultimately, I think weâll get more consistency from the approach we took.â
Editorâs note: See Golf course greens renovation advice for a distillation of research that can help you spearhead a greens renovation, minimize course closure and ensure a long-lasting finished product.
Which is not to say that, if the club had $10-12 million lying around for this project, Turner wouldnât have been happy to seed all the greens â and core them out, too, so as to replace their push-up profiles with USGA-specified profiles. But that was never the reality at Kenwood.
âIt would have been a thousand times easier to grow a green in from seed, but this was cheaper, and Iâm pretty sure weâll get more consistency across all 18 of our greens with the route we took,â Turner says. âYou have to adjust. The decision to go with slit drainage, for example. These push-up greens already drained well, with gravity. But when you take a green with 5% slopes and bring them down to 2%, you lose some of that help from gravity. So you need the slit drainage.â
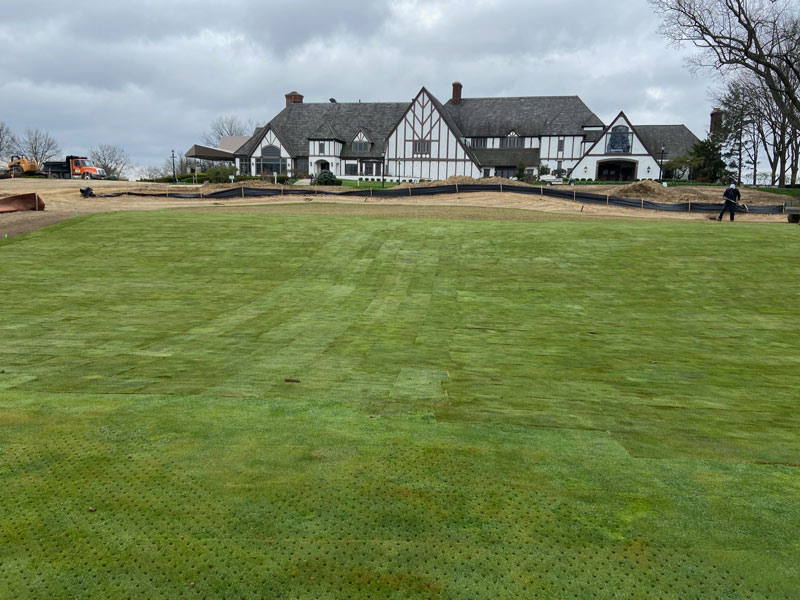
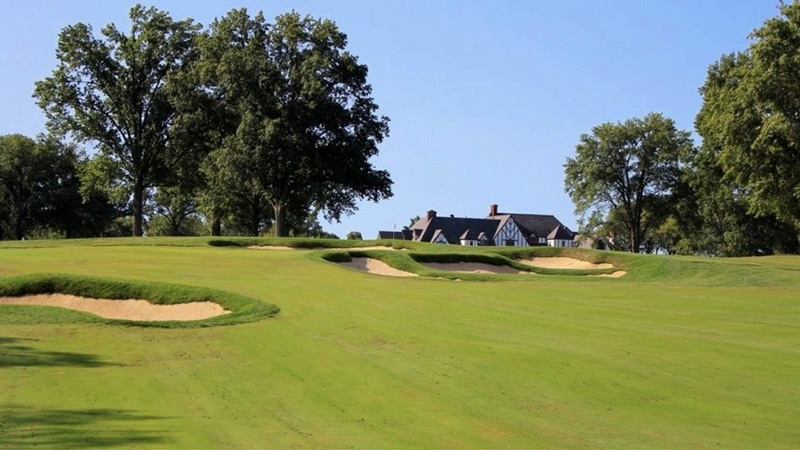
Newly sodded surfaces near Kenwoodâs clubhouse on April 1, 2020, during renovation work (top), and the clubhouse peeking out from beyond the Kendale Courseâs fourth green post-renovation (bottom).
Before his departure from Kenwood, Turner already saw changes in the turf heâd worked with intimately the past seven years, even if that turf had been moved from one hole to another â but donât ask him which turf came from where.
âSo, there are probably superintendents out there who are like quarterbacks, like Aaron Rodgers, who can remember every play and every audible from every game they played since college. I am not that guy. I have a hard time recalling exactly where all these green surfaces came from.
âBut Iâll tell you what, I can see theyâre behaving differently â mainly on account of the tree removal. That was a big driver of this project, and we did it, in part, to get rid of annual bluegrass. The back of our 17th green used to be 90% Poa, back there in the shade. The front was 90% bent. Once we removed the trees, we gave the bent a chance to better compete with that annual bluegrass. Poa in the open sun, especially here in Cincinnati, is going to struggle. Weâve already noticed significant reductions of Poa throughout by removing all the shade. There are PGRs out there that are way more effective on the Poa as compared to the bent. I expect weâll work to find the right ratio to help that process along. Supers have been doing that for years.â
Near the end of our conversation, in April, I asked Turner whether all of this renovation work â all the sod flipping, all the project management, all the disruption, on-the-spot decision-making and intensity â had been worth it. He hesitated before answering.
âThatâs a tough question. The painâs still awful fresh. ... If we didnât go through all that we did, if we had just done the standard $5 million rebunkering with new irrigation, we wouldnât have what we have today. The course is something really special now. But to think about doing it all again is a tough thing.â
Of course, the club is preparing to do it all again: Renovation of the Kenview Course is scheduled to begin in 2025. Turner, who resigned his post at Kenwood in late June, wonât be involved.
âWe owe a great debt to Kent Turner,â Petrick says, ânot just for his work during the renovation, but for close to a decade of service to club. Weâll worry about our work on the Kenview later, in the months to come. This summer and fall are dedicated to enjoying the Kendale. The members cannot get enough of it.â
Hal Phillips is the managing director of golf and resorts for Mandarin Media, a public relations firm with offices in Portland, Maine; Park City, Utah; and Ho Chi Minh City, Vietnam. He is the former editor of Golf Course News and a frequent contributor to GCM.