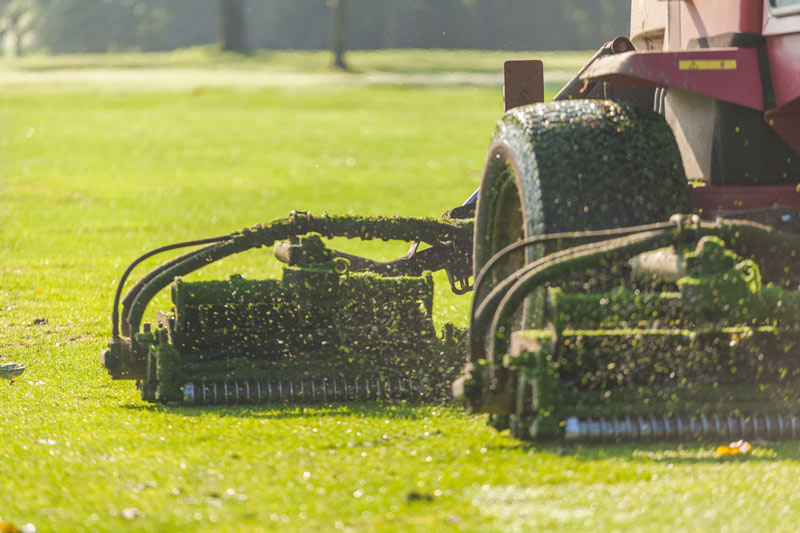
Changing mowing patterns from a traditional diagonal pattern to a “box” or “Zamboni” pattern — a tee-to-green, up-and-back method — is a strategy superintendents can employ to save time and money. Photo by Lukasz Szwaj/Shutterstock.com
There is always more than one way to do things on the golf course, and with labor costs on the rise and the unpredictable price of fuel, many superintendents are striving to improve efficiency in everything they do, including the way they mow fairways.
When done well, the long, diagonal mowing patterns on fairways can create a dramatic visual effect, but this does come with some drawbacks. Getting it right may be time-consuming, and while some employees can hop on a mower and pull it off in the first attempt, most will need many mowings to perfect the technique. Then there’s the considerable amount of time spent turning the mower around after each short pass across the fairway. This not only counts toward more time on the clock for operators, but also time on the mower’s hour meter, which means increased wear and tear, more rapid depreciation and greater fuel consumption.
To speed up the fairway mowing process, many superintendents have traded the diagonal striping of fairways for a more traditional up-and-back approach. This method is sometimes referred to as a “box” or “Zamboni” style, and it essentially involves push-cutting fairways in one direction from tee to green. There are agronomic, aesthetic and playability reasons for doing this, but the time and efficiency gains vs. diagonally striping seem to be the biggest motivations for switching. Adopting this tactic is not without challenges, though.
A change for the better
Jeff Ische, the GCSAA Class A superintendent at Golden Valley Golf and Country Club in Minneapolis, implemented the Zamboni mowing style in an effort to reduce wear and tear on his turf from turns in the rough, and also hoped to realize the various potential savings. After a season of mowing this way, the quality of the golf course’s rough had improved, but Ische’s operators were not consistently finishing the 27 acres of fairways in less time than when they were diagonally striping. On mornings with a heavy dew or rapid turf growth, Ische saved nearly 45 minutes per operator — almost three hours of combined labor for his four operators. However, on mornings with little or no dew, or after a dew drag and regulated growth, mowing fairways in such a fashion took as long if not longer than diagonally striping.
After watching the operators and jumping on the mowers himself, Ische realized that without the dew to create a contrast of dark and light stripes after mowing, seeing where the next pass should be was nearly impossible given that all the grass was being pushed the same direction. Even with average turf growth, those mornings with no dew were difficult.
Operators sometimes overlapped nearly an entire mower pass by trying to ensure they didn’t miss any grass. And even when attempting to overlap, areas of the fairway were still being neglected. Unfortunately, these areas weren’t always obvious, and many went unnoticed until the next day, creating problems if those days happened to host heavy play or a tournament.
Ische experimented with having a dedicated “lead mower,” with the next mower following right off his leading edge and the other two operators following close behind. This strategy worked most of the time, but it required a highly skilled operator to be the lead mower. The arrangement also led to inefficiencies in situations where only one or two mowers were necessary to finish that last pass down the fairway, which left the other operators waiting until that had been completed before moving on to the next hole. Another thought was to drag a weighted rope or chain behind each mower, but that idea didn’t get far because of concerns over leaving a mark on the fairway or the object getting caught up in one of the reels.
Brothers in arms
As Ische, a 20-year GCSAA member, talked over the predicament with his assistants, the suggestion to use a foam marker came up. Lead assistant Matt Olsonoski found a photo from a recent British Open showing mowers that appeared to be fitted with foam markers, which helped legitimize their plan. The Golden Valley grounds crew began experimenting by modifying an inexpensive foam marker previously used on their fertilizer spreaders.
Soon, Ische had an ally in this effort. Through his spray equipment parts supplier, Frost Inc., he learned that Rodney Johnson, CGCS, of Pine Hills Country Club in Sheboygan, Wis., had installed foam marker kits on two of his fairway mowers a couple of years earlier. The club had wanted to replace fairway striping with the more classic look of box cutting. Lightweight mowers mowing a striped pattern had changed the appearance of fairways, and in some ways, were a distraction from the course’s topography. Box cutting or Zamboni mow patterns would potentially be a time-saver as well.
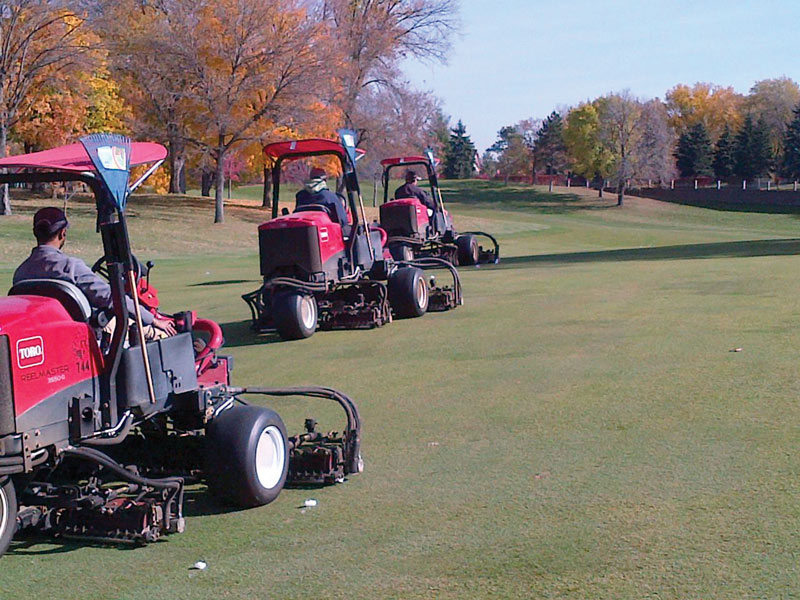
Installing foam markers on fairway units has increased the accuracy of operators mowing fairways at Golden Valley G&CC in Minneapolis and Pine Hills CC in Sheboygan, Wis. Photo courtesy of Frost Inc.
At Pine Hills, Johnson had faced many of the same challenges Ische was encountering. The adjustment in mowing pattern had been difficult for operators, and days with low quantities of dew on fairways — further complicated by the regular use of growth regulators — resulted in the same overlapping issues. It was a Pine Hills mower operator who observed that if they had foam marks like those supplied from a sprayer, the crew could eliminate a lot of overlapping. Johnson had foam marking kits from Frost Inc. installed on two of the three mowers normally used on the course, and developed a routine in which the three mowers followed one another. Not every mower needed to apply foam, but if each mower was equipped, then any machine could lead. The guidance from the foam has resolved any troubles with overlapping, and has given Pine Hills’ operators the confidence to execute superb mowing jobs.
Mowing made easier
Back at Golden Valley, with two of Ische’s four mowers equipped with foam markers, he split his operators into two teams, with each team using at least one mower with the marker kit. A foamless mower makes the first pass, and the operator with a foam marker follows right behind, leaving a line of foam balls for the lead mower to follow on the next trip down the fairway. Ische set up the markers so that the foam would be dropped on the outside edge of the outermost reels. Conveniently, the foam applied is rolled down by the overlap of the next mower, leaving nothing but a completely mowed fairway, done with as little overlap as possible.
The efficiencies gained via this mowing strategy are now achievable whenever Ische’s staff mows fairways, and saving three hours of labor and three hours of fuel consumption every time out has quickly offset the purchase price of the two foam marker kits. The foam markers used by both Ische and Johnson run about $500 each, and they were installed in about an hour or two. Kits come with two foam drops, one for each side of the mower, and a switch box for the operator control. The foam drops are mounted as low as possible to minimize error potentially caused by occasional wind. Foam concentrate is usually already on hand for use in sprayers, and the ongoing cost of the product is minimal. Based on the rate of foam use at Golden Valley, the 1-gallon tank on the foam marker system is sufficient for two fairway mowings.
The experienced operators at Golden Valley have embraced this change in fairway mowing, commenting on how much easier it now is to mow in the absence of dew. An added benefit? The foam markers also aid in the training of new operators. This technology isn’t new, but rather an example of clever superintendents adapting existing equipment for another purpose. With such innovations, the days of doing things the same old way on the golf course have certainly passed.
Ken Rost is the president and CEO of Frost Inc., a spray equipment parts company based in St. Croix Falls, Wis.