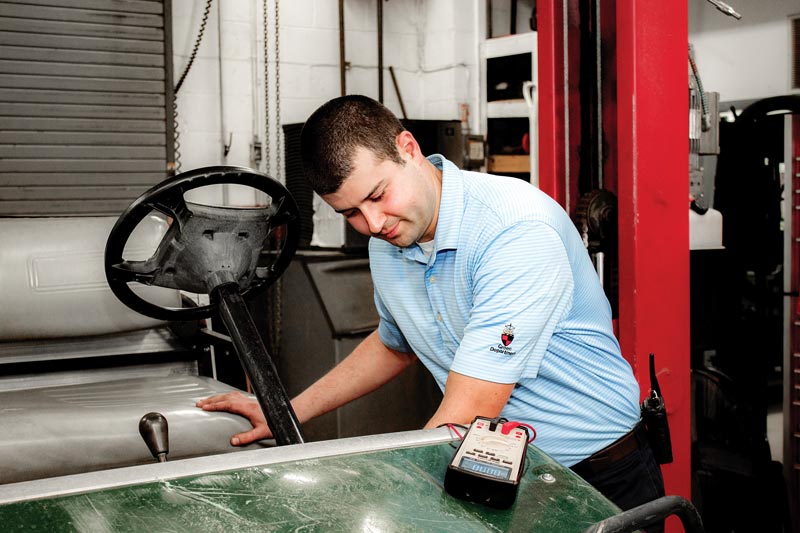
Tony Lewis, equipment manager at Chevy Chase (Md.) Club, credits good timing, good mentors and guidance from GCSAA for his advancement within the equipment manager profession. Photos by Jonathon Toto
I was lucky enough to begin my career in the golf course management industry three days after graduating from high school. I was eager to enlist in the armed forces but was waiting for a pivotal election in 2008.
Jay Nalls, superintendent at Norbeck Country Club in Rockville, Md., offered me a summer job assisting the club’s equipment manager, Brian Parker, around the shop. I had no formal mechanical experience, but Parker viewed this as an advantage, as he could teach me good habits from the beginning.
With encouragement from Nalls, shortly after I turned 20, I moved on to a job as the equipment manager at Hampshire Greens Golf Course in Silver Spring, Md., under superintendent Teddy Blauvelt. This was an exciting time for me, allowing me to learn as I went, to network with the eight other equipment managers at courses operated by the Montgomery Country Revenue Authority (MCRA), and to be advised by Stanley Kapulka, who at the time was the equipment program director and oversaw all nine courses.
The new job gave me the opportunity to have input on my yearly budget and was a leap, in my mind, toward becoming a true manager — someone with the ability to make key decisions and to seek consultation from other equipment managers.
Taking the next step
My education in the business up to that point had been largely of the on-the-job variety. For example, during this time at Hampshire Greens, I learned the importance of anticipation and subsequent planning. You usually mow greens, fairways and perimeters on Monday, Wednesday and Friday, right? Well, then it’s a good idea not only to inspect the reels and traction units after they’ve been used, but also to give that equipment a walk-around before active mornings. Know your fleet and the upcoming schedule so you can be the factor that ensures confidence in the equipment operation.
In 2015, GCSAA took on what the International Golf Course Equipment Managers Association (IGCEMA) had put a lot of effort into starting and created a membership classification specifically for equipment managers. The association also assumed management of a series of exams created by IGCEMA that allowed equipment managers to prove themselves and validate their skills.
After taking over administration of the IGCEMA exams, GCSAA began the process of reviewing, revising and, ultimately, expanding this program. What is now known as the Turf Equipment Technician Certification Program (TETCP) Level One consists of eight exams that cover core competencies key for all successful equipment managers. When completed, the program helps set a benchmark that shows an equipment manager is qualified to make the right diagnostic decisions and be efficient at the job.
A hidden benefit of these exams is seeing what areas you can build on. The opportunity for continued improvement through reading the study guides and working through the exams is a great way to build your career. I began taking the exams via a local Toro vendor who is a registered proctor.
Midway through the process of working on these exams, I stepped into the role of equipment program director for MCRA. Under the direction of Jon Lobenstine, the MCRA’s director of agronomy, I was responsible for assisting eight other equipment managers with troubleshooting, streamlining productivity via aggressive preventive maintenance plans, and overseeing vendor relations pertaining to equipment and our shops.
At 26, I found this a welcome challenge, as my experience was now at an accelerated pace thanks to the interactions I had with eight other courses and their equipment managers every day.
Membership has its privileges
I completed the eight TETCP Level One exams in the spring of 2017. Soon after I’d finished, I thought about how the majority of people in equipment manager positions wouldn’t have taken a written test since high school, and how that might factor into an equipment manager’s decision to tackle these exams.
That part of the process never bothered me, but I do sympathize with those who feel that way, because I have dealt with a speech impediment for most of my life. Public speaking is not my favorite thing to do, but, frankly, there are worse things in life. I applied to be a TETCP proctor with GCSAA in hopes of creating a comfortable atmosphere for applicants to take their exams with the support of a colleague who has been through the process himself.
After registering as an independent proctor, I began working with the team at GCSAA more and more, reviewing existing study materials and revising guides so readers could properly prepare for the new exams. This motivated me to apply for a term on the association’s Equipment Managers Task Group, and I was accepted. Going to GCSAA headquarters this past spring and working with this group was a fulfilling experience. Without a doubt, any problem could have been placed in that room, and we would’ve solved it together. I’d like every reader to know GCSAA has the best interests of every member in mind — something that was clearly illustrated to me during my visit.
The main duty put in front of the task group was to focus on the TETCP Level Two exams and the potential development of an equipment manager certification. We had to discern what testing objectives and abilities separated a technician from an actual manager. That included the “why” and not just the “how” behind equipment failure, implementing best management practices and safety standards in the workplace, and using diagnostic skills to prevent a problem from recurring. Rafael Barajas, CGCS, the chairman of this task group, and Kevin Sunderman, the vice chairman, along with GCSAA staff, were a huge help. They provided the group with impartial views and, at times, encouragement to get us through the process.
Working with a psychometrician — someone who practices the science of educational and psychological measurements — to develop the Level Two exam questions was fascinating. Learning how to word a question and offer solutions that could be understood only by someone who truly knew the material made the process fair but clinical. As a team, the task group worked through what are important distinctions between technicians and managers. The psychometrician did an excellent job understanding our ideas and then translating them into peer review for exam development.
Increased experience, knowledge
After my visit to GCSAA headquarters, I was lucky enough to transition to a new position with Chevy Chase Club, to work with Dean Graves, CGCS, and Chris Sandels, the assistant golf course manager. We work hard together so that a well-managed team can provide superb playing conditions for our members.
I am fortunate to have Walter Miles with me in the shop, and I look forward to training as many assistants as possible in the coming years. One thing this industry needs is new, well-trained technicians.
Something I began to focus on at Hampshire Greens and have continued to emphasize at Chevy Chase Club is the relationship with the operators. We encourage any and all feedback from operators when machines are parked outside the shop for inspection. Having an open and easygoing dialogue helps operators explain a problem or an incident. I certainly prefer to know about an issue before seeing it the next time the machine goes out.
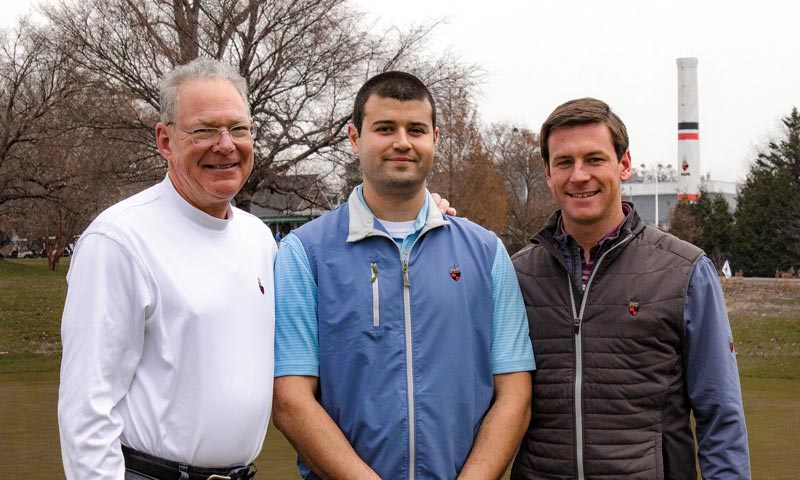
At Chevy Chase Club, Lewis (center) works with 38-year GCSAA member Dean Graves, CGCS, (left) and assistant course manager Chris Sandels (right), a nine-year association member.
One time, an operator mentioned he’d had the hardest time cutting straight lines on a triplex that morning. He could drive fine between passes, but with the reels down, it was “bananas.” It turns out the frame at the steering cylinder mount was cracked in half. The reel lift cylinder would hold it together when raised, but it could wobble and shake with the reels down.
At Chevy Chase Club, I’ve also learned the value of daily field checks, which take place here in conjunction with our different assistant golf course managers. Miles and I work jointly with them to confirm the safety of the operator, that machines are working properly, and that after-cut appearance is acceptable. We hold monthly safety meetings during which we promote proper operation and care of different machines. Topic examples are proper lifting, small rotary operation, why safety switches are on machines, and safe pathways for traveling to and from the maintenance shop. Creating protocols and correct safety procedures such as these are testing objectives for the TETCP Level Two exams.
Continued progress for equipment managers
Down the road, an equipment manager certification may take the form of a portfolio program with peer review, similar to GCSAA’s Certified Golf Course Superintendent program. I promote the TETCP exams and study protocol because I want to see a uniform advancement in the position and career path. Every resource is available on GCSAA’s Equipment Management page, from educational videos, worksheet templates, forums and study guides to a constantly growing class arrangement at the Golf Industry Show.
Whether you are a superintendent with an equipment manager who may not know about these opportunities or an equipment manager on the fence about whether to get more involved, I advise all equipment managers to take the next step in their involvement with GCSAA.
Now is a pivotal point in our business, with budgetary pressures, changes to government standards and increased competition. GCSAA membership and passing these TETCP exams will benefit your career and advance the standing of those who come after you.
Tony Lewis is the equipment manager at Chevy Chase (Md.) Club and a five-year member of GCSAA.